CASE STUDY
Achieving At Source Cleaning for the First Time
Oil & Gas
CLIENT
UK Operator
LOCATION
UK, North Sea
SERVICES
Mechanical Separation
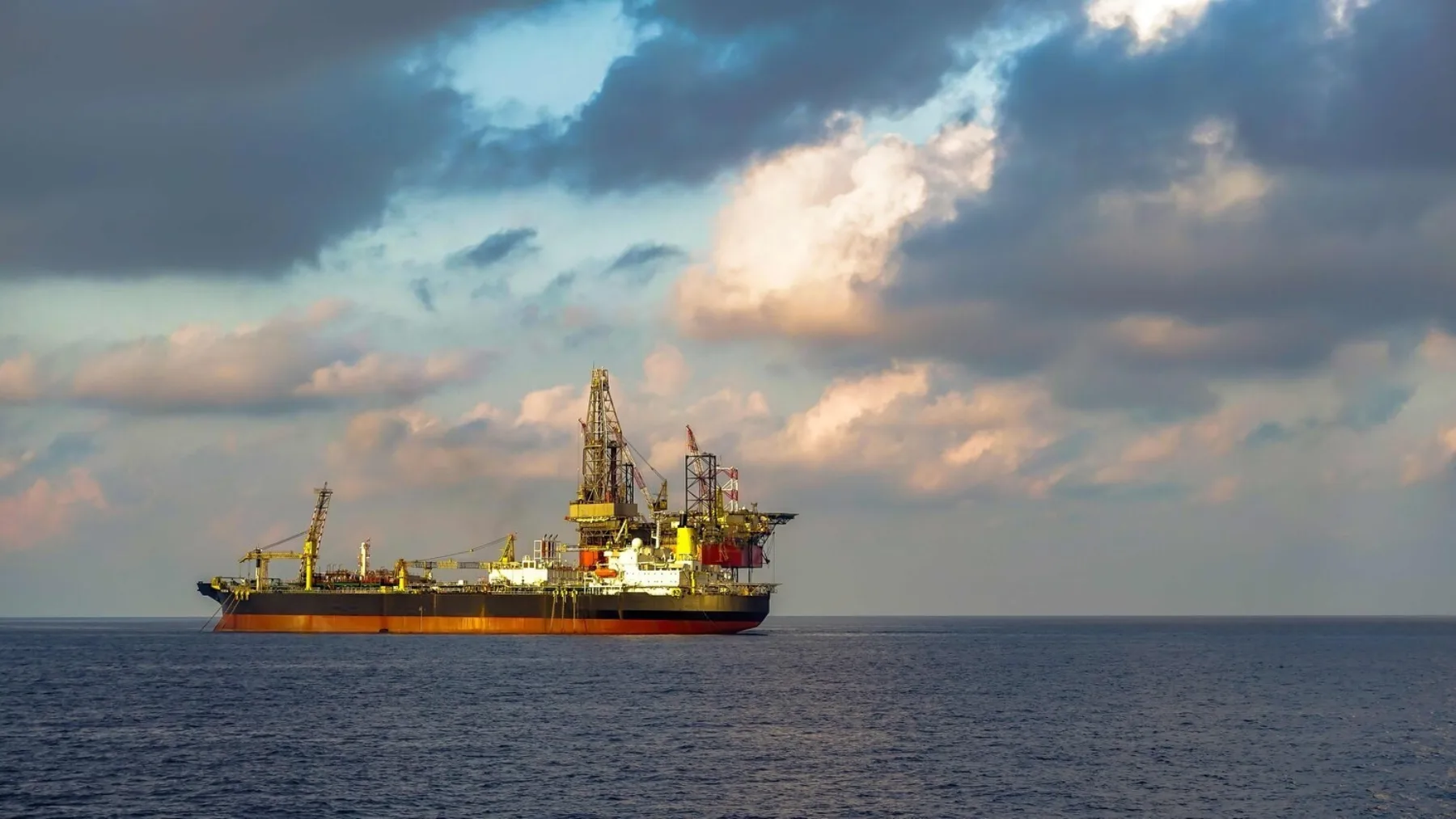
While feeding the centrifuge with a port slop pump, surging of fluid was observed, which meant it was not possible to achieve a stable flowrate, to overcome this a back pressure was introduced on the slop water return line.
RESULTS
This was the first time our client had a fully functioning slops system on board their FPSO allowing them to treat slops at source. Our inspection results post installation found all valves and functions to be working correctly. By implementing such a system enabled our client to realise long term commercial and environmental benefits. All works were carried out on time, without any LTIs and within budget.
POWERFUL BENEFITS
- Improved wastewater treatment
- Reduced wastewater environmental and commercial burdens
- Future recommendations for continued improvement
- Zero LTIs
THE CHALLENGE
Our client, a UK operator, required their slops units to be operational prior to seeing first oil. To achieve this meant working to a compressed timeframe and delivering a solution that would enable all slops to be cleaned “at source”, which had previously not been thought possible.
HOW WE HELPED
The slop water centrifuge was installed in the shipyard but was never fully commissioned. To get the slop water centrifuge back up to operational readiness, a detailed survey was conducted, allowing us to identify all underlying issues. From here we removed and replaced all corroded parts including valves, O-rings, spindles and more.
The control system had to be commissioned from a nonfunctioning state to fully operational including integration with central control room.
CONTACT OSSO
Got a question
about a project?
Related Case Studies
Geothermal drilling achieving a 25% temperature reduction
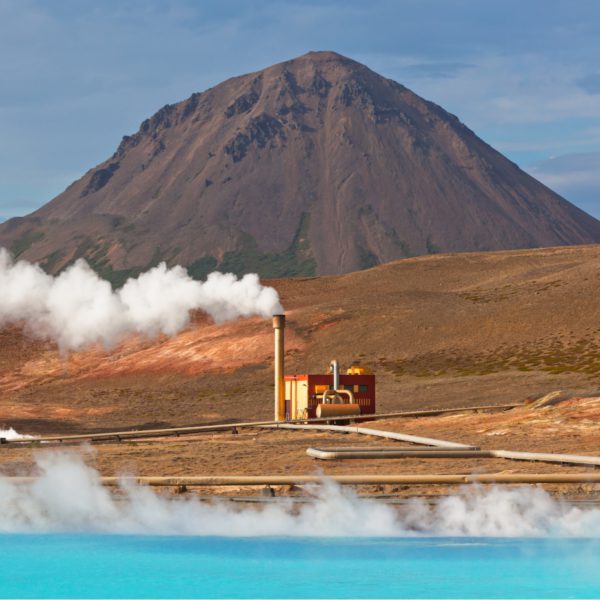
- 25% temperature reduction
- Full-service maintenance contract
- Annual equipment swap out and refurb programme
Improve drilling efficiencies in high temperature wells.
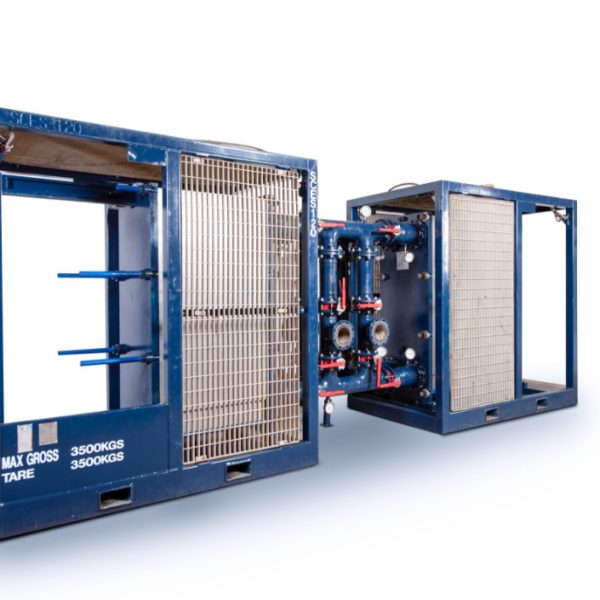
- Reduced days drilling NPT per section drilled
- 40% decrease in round trips per section drilled
- 95% reduction in tool DBR