CASE STUDY
Malthouse Full
PHE Overhaul
Food & Drink
CLIENT
Major Distillery Group
LOCATION
Burnhead
SERVICES
Plate Heat Exchanger
Service
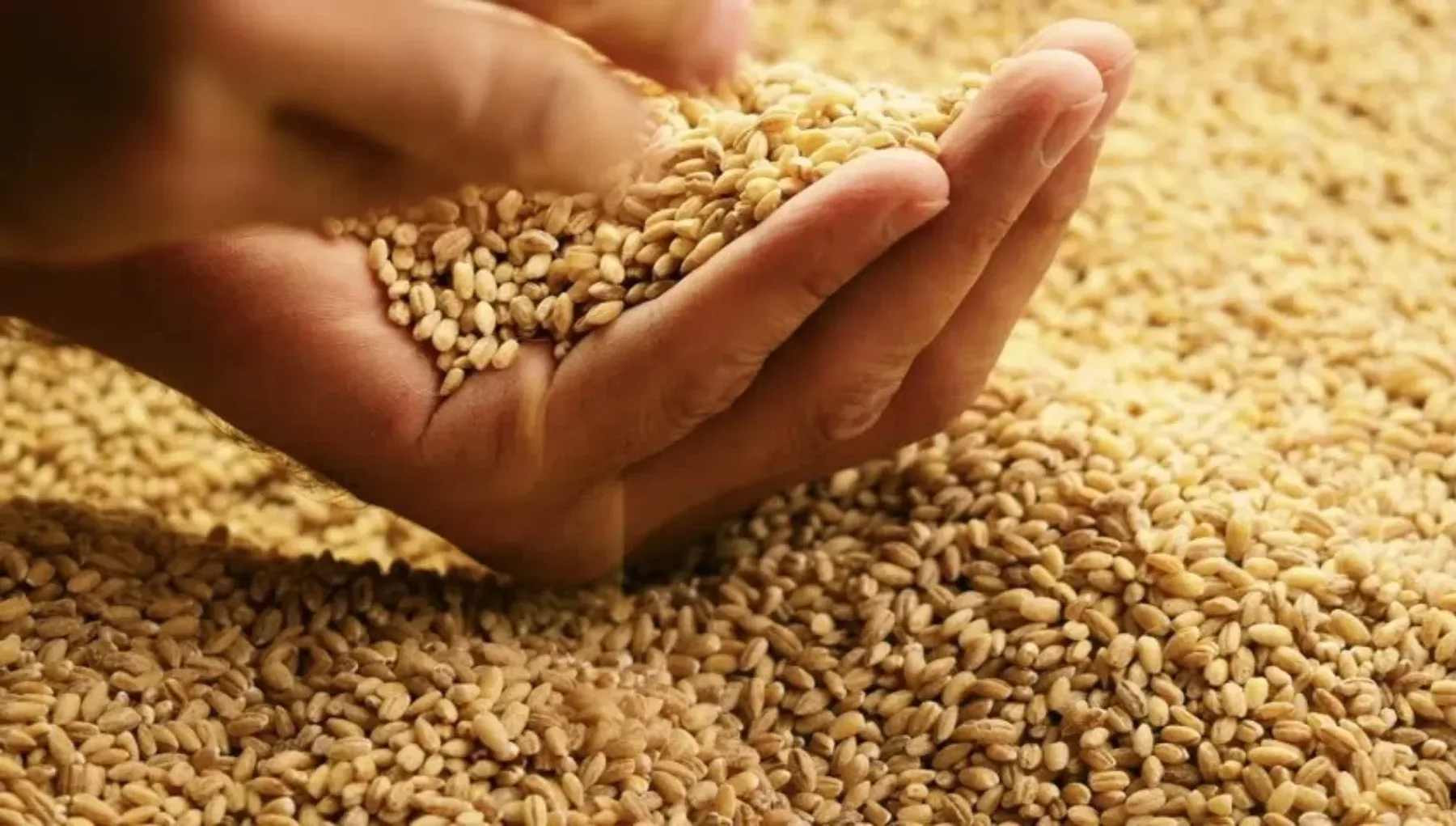
THE CHALLENGE
As part of a planned service and maintenance schedule, a major UK malthouse owner had the need for significant maintenance and repair requirements of their PHEs.
OSSO conducted an initial thermographic survey which found that the Glycol/hot water PHE in the heat loop building within the maltings was performing poorly due to internal fouling.
Failure to address this would ultimately result in the system malfunctioning, causing significant production loss.
HOW WE HELPED
OSSO carried out an on-site thermographic survey as part of our preventative maintenance programme and in accordance with the client's planned silent season.
The outcomes of this identified the problems, enabling prompt action and a comprehensive overhaul of the plates, which included the following:
- PHE disassembly
- Chemical cleaning
- Sourcing of parts
- NDT inspection
- Pressure testing
- Dye penetration checks
- Re-gasketing
- Install of refurbed plate packs
"Communication was excellent, swift, good organisation with a willingness to listen…I saw personnel behaving pleasantly and safely on the job and while on site. Good quality of work."
RESULTS
The work scope was successfully finished within the distillery's 'silent season' window, ensuring the least possible disruption to production time.
- Completed within the scheduled 5-day 'silent season' inclusive of onsite and offsite work
- All works completed and carried out in house ensuring full project control
- Extended the life of the existing plate packs
- Improved the overall efficiency of the heat exchanger
CONTACT OSSO
Got a question
about a project?
Related Case Studies
Geothermal drilling achieving a 25% temperature reduction
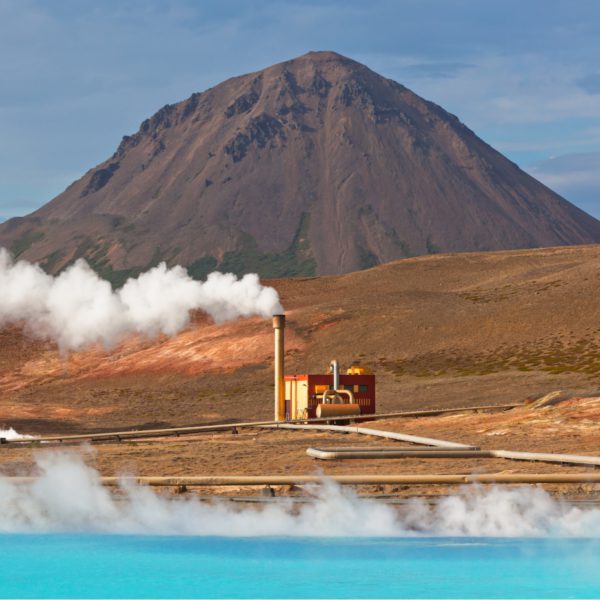
- 25% temperature reduction
- Full-service maintenance contract
- Annual equipment swap out and refurb programme
Improve drilling efficiencies in high temperature wells.
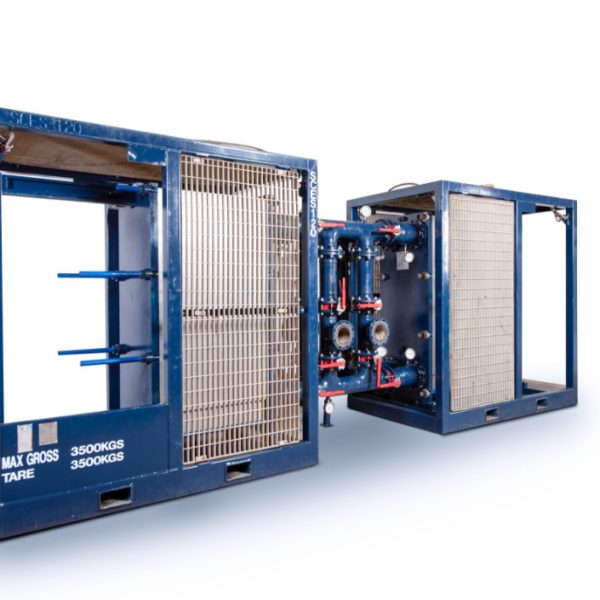
- Reduced days drilling NPT per section drilled
- 40% decrease in round trips per section drilled
- 95% reduction in tool DBR